Your cart is currently empty!
Case Studies: Success Stories of Companies Implementing Proactive Maintenance
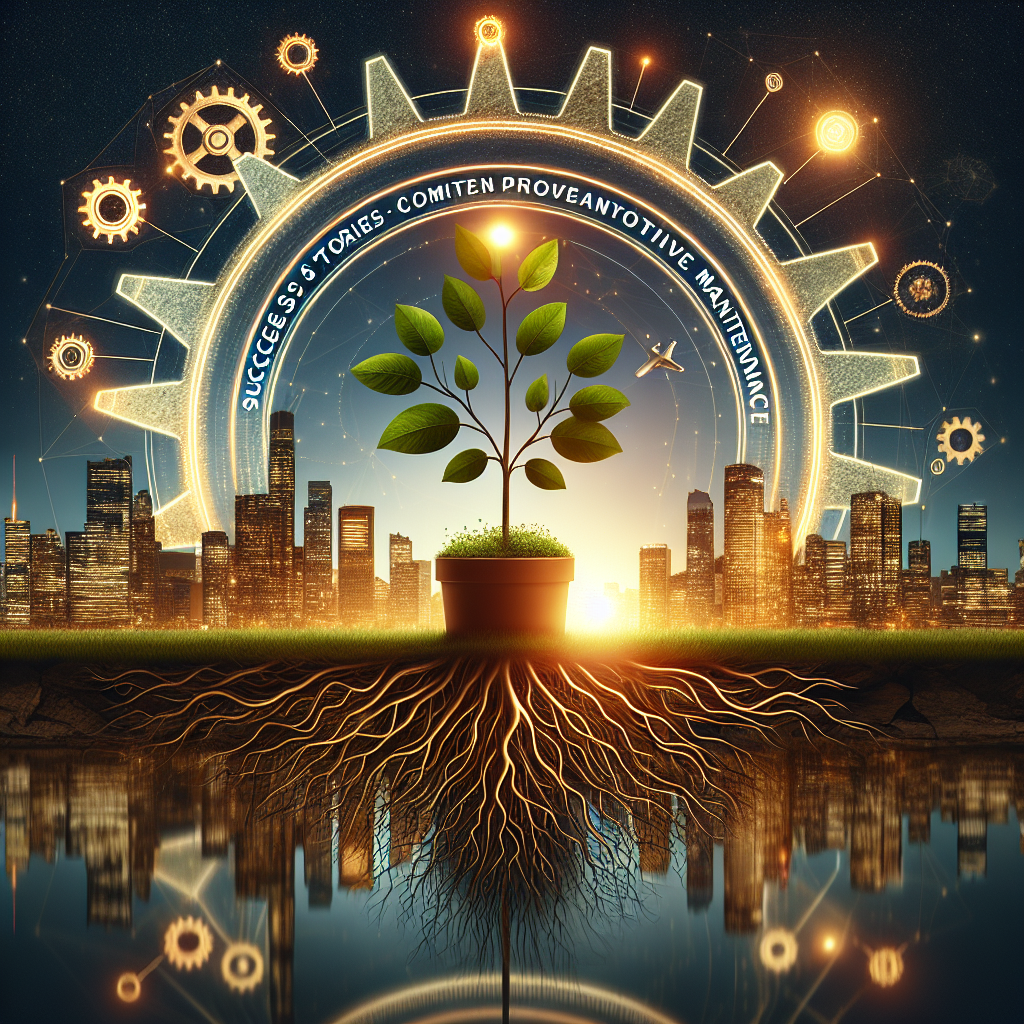
Proactive maintenance is a strategy adopted by many companies to prevent equipment failures and downtime by identifying and addressing potential issues before they escalate. This approach has proven to be highly effective in reducing costs and increasing efficiency for businesses across various industries.
One of the most well-known success stories of proactive maintenance is that of Delta Airlines. The airline implemented a proactive maintenance program for its fleet of aircraft, which resulted in a significant reduction in maintenance costs and downtime. By using data analytics and predictive maintenance technologies, Delta was able to identify potential issues before they became major problems, allowing them to schedule maintenance at convenient times and avoid costly unplanned maintenance.
Another success story is that of Toyota Motor Corporation. The automotive giant implemented a proactive maintenance program in its manufacturing facilities, leading to a significant increase in production efficiency and a reduction in equipment downtime. By regularly monitoring equipment performance and implementing preventative maintenance measures, Toyota was able to improve the overall reliability of its production processes and reduce the risk of equipment failures.
In the pharmaceutical industry, Merck & Co. has also seen success with proactive maintenance. The company implemented a predictive maintenance program for its manufacturing equipment, which helped them identify and address potential issues before they impacted production. As a result, Merck was able to reduce downtime and increase the overall reliability of its manufacturing processes, leading to improved product quality and customer satisfaction.
Overall, the success stories of companies implementing proactive maintenance highlight the benefits of taking a proactive approach to equipment maintenance. By investing in predictive maintenance technologies and regularly monitoring equipment performance, businesses can reduce costs, increase efficiency, and improve the overall reliability of their operations. As technology continues to advance, proactive maintenance will become increasingly important for companies looking to stay competitive in today’s fast-paced business environment.
Leave a Reply