Your cart is currently empty!
From Reactive to Proactive: How to Transition Your Maintenance Approach
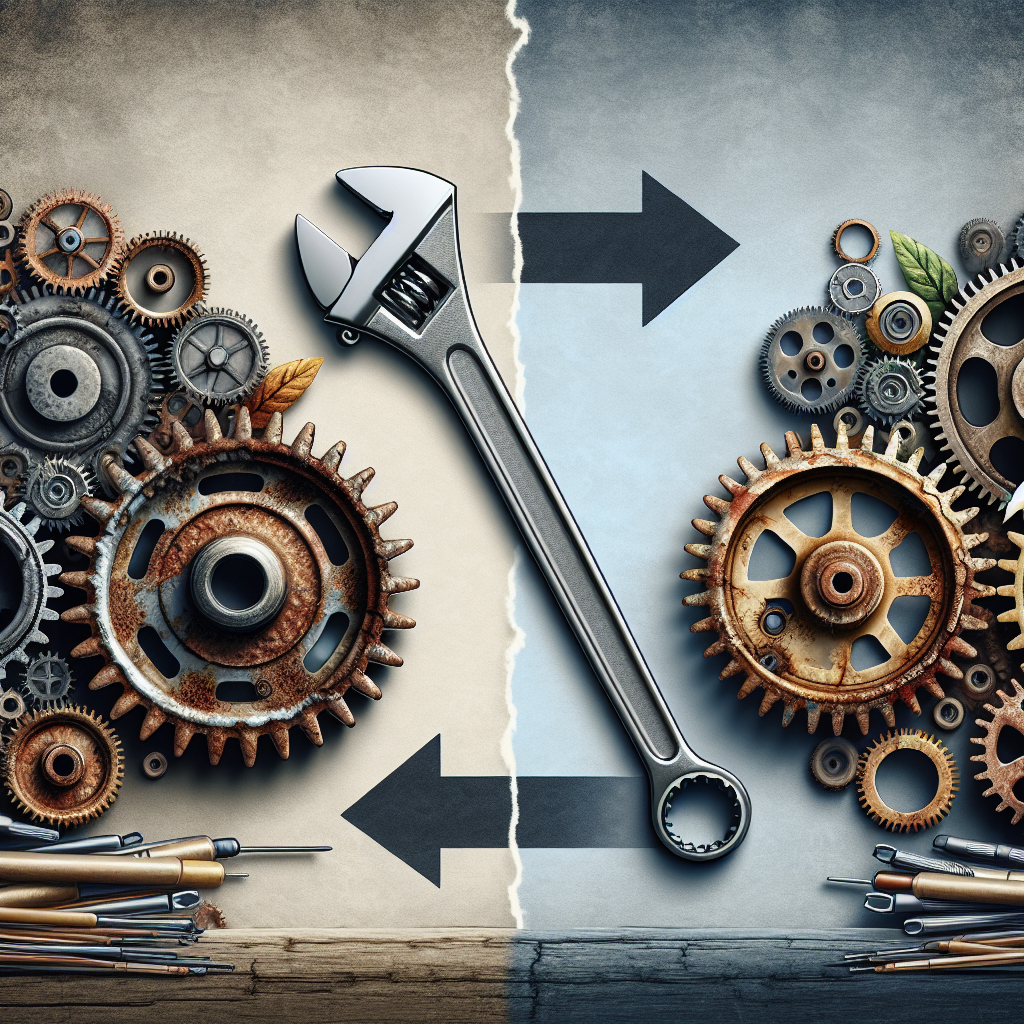
Maintenance is a crucial aspect of keeping equipment and facilities running smoothly and efficiently. In the past, maintenance has often been a reactive process, where issues are only addressed once they have already caused a problem or breakdown. However, this approach can lead to costly downtime, repairs, and potential safety hazards. To avoid these issues, many organizations are now transitioning to a proactive maintenance approach.
Proactive maintenance involves anticipating potential issues before they occur and taking preventive measures to address them. This shift in mindset can help organizations save time and money in the long run by avoiding costly repairs and downtime. Here are some steps you can take to transition from a reactive to a proactive maintenance approach:
1. Conduct regular inspections and assessments: Regularly inspecting equipment and facilities can help identify potential issues before they become major problems. This can include checking for signs of wear and tear, leaks, or other issues that could lead to a breakdown.
2. Implement a preventive maintenance schedule: Create a schedule for routine maintenance tasks, such as changing filters, lubricating moving parts, or cleaning equipment. By following a preventive maintenance schedule, you can address minor issues before they escalate into major problems.
3. Invest in technology: Utilize technology such as sensors, monitoring systems, and predictive maintenance software to track equipment performance and predict potential issues. These tools can help you identify trends and patterns that can indicate when maintenance is needed.
4. Train your team: Ensure that your maintenance team is properly trained on proactive maintenance techniques and best practices. Provide ongoing training and support to help them identify potential issues and take preventive action.
5. Establish key performance indicators: Set key performance indicators (KPIs) to measure the effectiveness of your proactive maintenance program. Track metrics such as equipment uptime, maintenance costs, and mean time between failures to evaluate the success of your efforts.
By transitioning from a reactive to a proactive maintenance approach, organizations can improve equipment reliability, reduce downtime, and increase operational efficiency. While the shift may require an initial investment of time and resources, the long-term benefits can far outweigh the costs. By implementing regular inspections, preventive maintenance schedules, technology, training, and KPIs, organizations can proactively address maintenance issues and ensure that their equipment and facilities are running smoothly and efficiently.
Leave a Reply