Your cart is currently empty!
Proactive Maintenance Best Practices: A Guide for Facility Managers
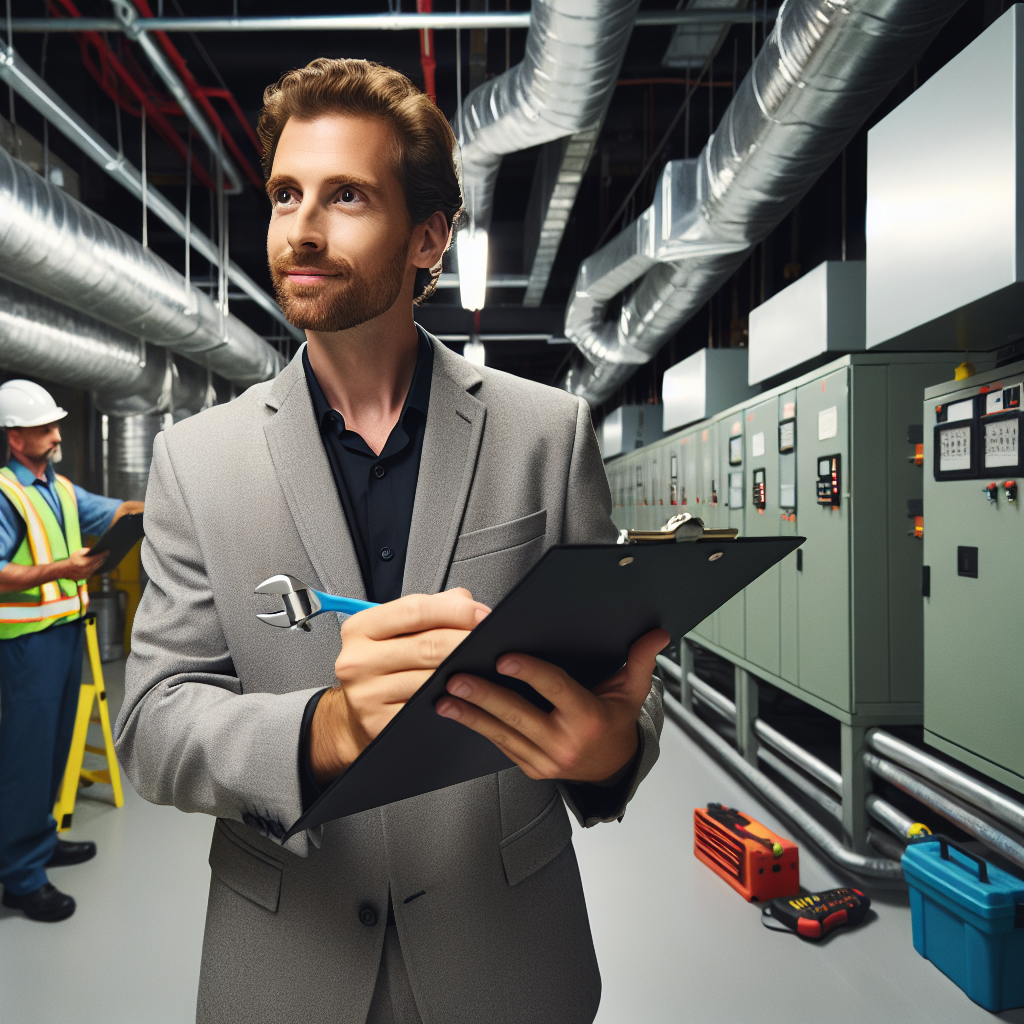
As a facility manager, ensuring that your building’s equipment and systems are well-maintained is crucial for the smooth operation of your facility. Proactive maintenance is key to preventing costly breakdowns and ensuring that everything is running efficiently. In this guide, we will discuss the best practices for proactive maintenance that facility managers should follow.
1. Develop a Maintenance Plan: The first step in proactive maintenance is to develop a comprehensive maintenance plan for your facility. This plan should outline all the equipment and systems that need regular maintenance, as well as the frequency of maintenance tasks. By having a detailed plan in place, you can ensure that all necessary maintenance tasks are being carried out on time.
2. Conduct Regular Inspections: Regular inspections are essential for identifying any potential issues before they escalate into more significant problems. Facility managers should schedule regular inspections of all equipment and systems to check for signs of wear and tear, leaks, or other issues. By catching problems early, you can prevent costly repairs and downtime.
3. Implement Preventive Maintenance: In addition to regular inspections, facility managers should also implement preventive maintenance tasks to keep equipment and systems running smoothly. This includes tasks such as lubricating moving parts, replacing filters, and checking fluid levels. By staying on top of preventive maintenance tasks, you can extend the life of your equipment and reduce the risk of unexpected breakdowns.
4. Train Staff: Properly trained staff are essential for proactive maintenance. Facility managers should ensure that their maintenance staff is well-trained in the proper maintenance procedures for all equipment and systems in the facility. By investing in training, you can ensure that maintenance tasks are performed correctly and efficiently.
5. Use Technology: Technology can be a valuable tool for proactive maintenance. Facility managers can use software programs to track maintenance schedules, generate work orders, and keep detailed maintenance records. Additionally, sensors and monitoring systems can be used to track equipment performance in real-time and alert facility managers to any issues that may arise.
6. Prioritize Safety: Safety should always be a top priority when performing maintenance tasks. Facility managers should ensure that all maintenance staff are following proper safety protocols and using the necessary personal protective equipment. By prioritizing safety, you can prevent accidents and injuries during maintenance activities.
In conclusion, proactive maintenance is essential for facility managers to keep their buildings running smoothly and efficiently. By developing a comprehensive maintenance plan, conducting regular inspections, implementing preventive maintenance tasks, training staff, using technology, and prioritizing safety, facility managers can ensure that their facility is well-maintained and operating at its best. By following these best practices, facility managers can prevent costly breakdowns, extend the life of their equipment, and ensure the safety of their staff and occupants.
Leave a Reply