Your cart is currently empty!
Proactive Maintenance Best Practices for Long-Term Equipment Reliability
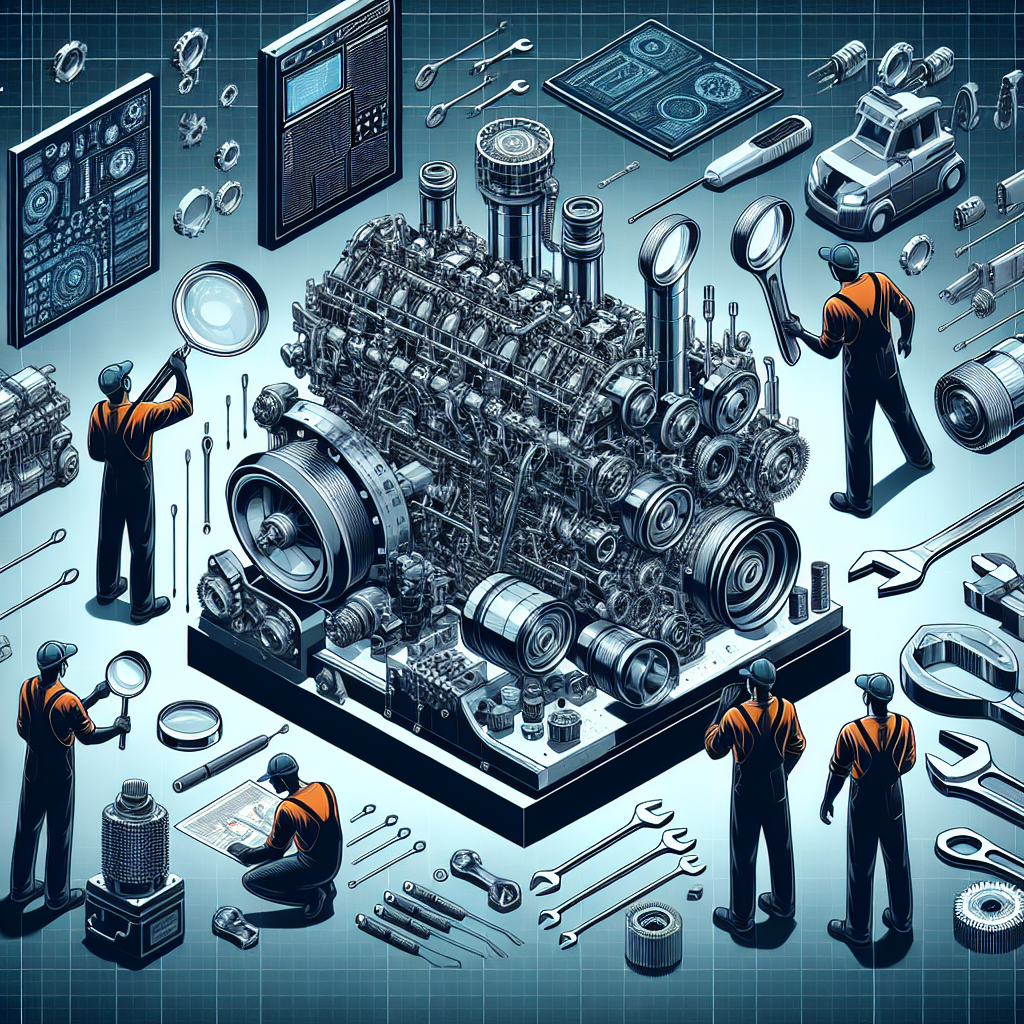
Proactive maintenance is a key practice in ensuring the long-term reliability of equipment. By implementing proactive maintenance best practices, organizations can prevent breakdowns, reduce downtime, and extend the lifespan of their equipment. In this article, we will discuss some of the best practices for proactive maintenance that can help organizations achieve long-term equipment reliability.
1. Develop a maintenance schedule: One of the first steps in implementing proactive maintenance is to develop a maintenance schedule for each piece of equipment. This schedule should outline the frequency of maintenance tasks, such as inspections, lubrication, and calibration, as well as the specific tasks that need to be performed. By following a regular maintenance schedule, organizations can identify and address potential issues before they lead to equipment failure.
2. Conduct regular inspections: Regular inspections are essential for identifying potential issues early on. Inspections should be conducted by trained personnel who are familiar with the equipment and its maintenance requirements. During inspections, personnel should look for signs of wear and tear, leaks, loose fittings, and other issues that could impact the reliability of the equipment.
3. Keep detailed maintenance records: Keeping detailed maintenance records is crucial for tracking the maintenance history of each piece of equipment. These records should include information such as maintenance tasks performed, parts replaced, and any issues that were identified during inspections. By maintaining accurate records, organizations can track the performance of their equipment over time and identify trends that may indicate potential issues.
4. Implement predictive maintenance techniques: Predictive maintenance techniques, such as vibration analysis, thermography, and oil analysis, can help organizations predict when equipment failure is likely to occur. By monitoring key indicators of equipment health, organizations can identify potential issues before they lead to breakdowns and take corrective action to prevent costly repairs.
5. Train maintenance personnel: Proper training is essential for ensuring that maintenance personnel are equipped to perform proactive maintenance tasks effectively. Training should cover topics such as equipment operation, maintenance procedures, and safety protocols. By investing in training for maintenance personnel, organizations can ensure that maintenance tasks are performed correctly and efficiently, leading to improved equipment reliability.
6. Invest in quality parts and materials: Using quality parts and materials is essential for maintaining the reliability of equipment. Low-quality parts can lead to premature failure and costly repairs, while high-quality parts can help extend the lifespan of equipment. Organizations should work with reputable suppliers to ensure that they are using parts and materials that meet the required specifications for their equipment.
In conclusion, proactive maintenance is essential for ensuring the long-term reliability of equipment. By following these best practices, organizations can prevent breakdowns, reduce downtime, and extend the lifespan of their equipment. By developing a maintenance schedule, conducting regular inspections, keeping detailed maintenance records, implementing predictive maintenance techniques, training maintenance personnel, and investing in quality parts and materials, organizations can achieve long-term equipment reliability.
Leave a Reply